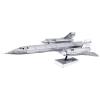
[GBC] The Akiyuki Project (2010 - 2020)
By
Blakbird, in LEGO Technic, Mindstorms, Model Team and Scale Modeling
-
Recently Browsing 0 members
No registered users viewing this page.
By
Blakbird, in LEGO Technic, Mindstorms, Model Team and Scale Modeling
No registered users viewing this page.