-
Posts
496 -
Joined
-
Last visited
About Splat
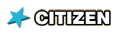
Spam Prevention
-
What is favorite LEGO theme? (we need this info to prevent spam)
Technic
Profile Information
-
Gender
Not Telling
Extra
-
Special Tags 1
https://www.eurobricks.com/forum/public/style_images/tags/technic_gold.png
Recent Profile Visitors
-
[GBC] To and Fro
Splat replied to Splat's topic in LEGO Technic, Mindstorms, Model Team and Scale Modeling
Thanks for your work on this Aron. Unfortunately the PDF instructions have a few issues. There are quite a few steps where pieces are just 'floating', and others where the pieces can't be put together in that order. There are also a lot of steps where the parts are individual segments of the wires and string rather than the wire/string as one piece, and where the part call-outs are on top of the model image/s.- 41 replies
-
- gbc
- great ball contraption
-
(and 2 more)
Tagged with:
-
Splat started following Using non-LEGO tools to build with LEGO technic [video] , Pendulum wave music machine , [APP] BrickController2 and 7 others
-
Pendulum wave music machine
Splat replied to aeh5040's topic in LEGO Technic, Mindstorms, Model Team and Scale Modeling
I love the beautiful artwork that you create. -
[APP] BrickController2
Splat replied to imurvai's topic in LEGO Technic, Mindstorms, Model Team and Scale Modeling
@imurvai - Is it possible to use BC2 with bluetooth keyboards? I have a bluetooth keyboard that has arrow keys as well as a full keyboard and a mouse trackpad. I can use this keyboard as an input device for my phone/smart TV/etc. When I open Game Controller KeyMapper > Assign Controller, it recognises my bluetooth keyboard as a "controller", and I can see the values for the key presses. However, when I open BC2 > Controller Tester, it doesn't recognise any of the key presses. I think that this is because the keyboard isn't really a "gamepad" input device. Could BC2 be extended to work with bluetooth keyboards in addition to gamepads? This is the bluetooth keyboard that I'm using: https://www.amazon.com.au/gp/product/B015J6TEN8- 1,288 replies
-
- sbrick
- game controller
-
(and 8 more)
Tagged with:
-
GBC General Discussion
Splat replied to Jim's topic in LEGO Technic, Mindstorms, Model Team and Scale Modeling
Thanks Rohan. I actually made two separate (yet similar videos). Constant Velocity (from motor) to Variable Velocity (when universal joints are misaligned): Constant Velocity (from motor) to Constant Velocity (when universal joints are aligned correctly): The descriptions on each video on the YouTube page has more information. I first came across this 'variable velocity' issue when building 8043, where misaligned universal joints would make the bucket shake around a bit. I do plan on making another video explaining these a bit more and also comparing to CV Joints... one day. PS. Here's the link to the other thread discussing universal joint alignment: https://www.eurobricks.com/forum/index.php?/forums/topic/49999-universal-joints-question-for-technic-experts/- 1,112 replies
-
Hi @UrielC, I'm glad you like my Minifig display stands, and that you have been able to adapt it to fit different numbers of Minifigs. I have sent you a message.
-
@Nightfall - Nice re-interpretation of my Mini Modular Modern Office Building At this larger scale, you have packed in some great little details. I especially like all the pieces of furniture, the floor tiling on the first (ground) floor and the fourth floor, the elevator in the corner, the way that you keep the walls and windows SNOT'd like I had in my Mini Version, and the way you used the leaf pieces on the first (ground) floor to cover up the anti-studs. I also love that dust bin (trash can) design on the first (ground) floor and the roof terrace! Here are the two models side-by-side:
-
If your photos are coming out too 'yellow orange', perhaps you can adjust the white balance of your camera accordingly. Most (all?) digital cameras will let you do this - check your camera settings or read the manual. I'm not sure which camera/flash you are using, but in your flash example it seems that either something was blocking the flash, the flash was too far away from the subject, or the flash was set to a very low level. In your last example with the daylight bulb you are still getting harsh shadows. I would recommend using multiple diffuse light sources to get better results. If you only have one light, you can use a white piece of card to 'bounce' some light back into your model from the other side to fill in the shadows a little bit. My recommendation for the best way to get decent photos is to use a sturdy tripod or other similar support for your camera. This will allow you to take decent photos with a wide variety of lighting conditions. As an example, I have even managed to take great looking photos using just a very low powered flashlight/torch with an incandescent bulb to light the model (that's all that I had access to at the time). I set my camera's white balance to match the colour temperature of the flashlight/bulb (to get 'white' whites), used a tripod for my camera, and set my camera to a long exposure (30 seconds). I then used the flashlight/torch to 'paint' light onto the model from various angles over the 30 second exposure time. Continuously moving the flashlight/torch helped to eliminate any harsh shadows. This just goes to show that you don't 'need' fancy lighting setups to light your models, but they do help to make things quicker and more predictable.
-
Santa spending some time on the beach in the summer sunshine 'down-under' this Christmas:
-
Quadruped kinematic workbench
Splat replied to oracid's topic in LEGO Technic, Mindstorms, Model Team and Scale Modeling
Your screen capture software is fine and does a good job. I just wanted to let you know of Linkage Simulator's option to export to video in case you weren't aware of it. Either way works well. -
Quadruped kinematic workbench
Splat replied to oracid's topic in LEGO Technic, Mindstorms, Model Team and Scale Modeling
@oracid - Those are some interesting walking mechanisms. I like how the foot lifts up quickly and goes down quickly, leaving more time for the foot to be on the ground. I'm glad that you found that Linkage Simulator software to be useful, and it looks like you have mastered it pretty quickly. FYI: you can also export videos directly from the software (rather than using another screen capture program). On my computer I did have to install x264VfW to get it to export videos properly. -
Question about gears and chains
Splat replied to paupadros's topic in LEGO Technic, Mindstorms, Model Team and Scale Modeling
All Technic gears (since about 1977) are designed to work with each other, so the gear teeth have the same pitch allowing them to mesh together, and this constant pitch also means that the chain links will work on all of the gears that others have mentioned above. Technic gears can generally be divided into two categories: Gears with skinnier square teeth (8, 16, 24, 40), and Gears with fatter rounded (bevel) teeth (12, 20, 36). The chain links will work with all of the skinner square teeth gears, except the newer 8 tooth gears as Void_S mentioned. The size of a gear can be calculated by the number of teeth divided by 8. 8 tooth gear / 8 = 1 stud 16 tooth gear / 8 = 2 studs 24 tooth gear / 8 = 3 studs 40 tooth gear / 8 = 5 studs Since the teeth of one gear overlap with the teeth of the adjacent gear, the true diameter is a little bit bigger than these values. For example, the true diameter of a 24 tooth gear = 3 studs + the width of a gear tooth, meaning that it won't fit in a 3x3 stud hole, but it will mesh with another gear next to it. The number of teeth can also be used to work out the spacing required between gears: (gear1 + gear2) / 2 gears / 8 teeth. 8 tooth gear to 8 tooth gear: (8+8) / 2 / 8 = 1, meaning that these two gears should be 1 stud apart (center to center) 24 tooth gear to 40 tooth gear: (24+40) / 2 / 8 = 4, meaning that these two gears should be 4 studs apart (center to center) If you are trying to mesh two gears that are diagonal from each other, the same rules applies but you might have to use some Pythagoras geometry to work out the distances and gears that will fit, or use Sariel's gear calculator: http://gears.sariel.pl/ -
Quadruped kinematic workbench
Splat replied to oracid's topic in LEGO Technic, Mindstorms, Model Team and Scale Modeling
Nice work. So much can be done with some nice linkage mechanisms (walkers, GBC modules, factory machines, etc). As you mentioned, each pivot can have almost infinite adjustments, leading to almost infinite paths that can be made. This video from Disney Research Hub is also good to watch: For a good computer linkage simulator I can recommend this one: http://blog.rectorsquid.com/linkage-mechanism-designer-and-simulator/ It allows you to quickly and easily make simple or complex mechanisms, and allows you to trace the various points in the mechanism. It is 2D, so trying to replicate things such as worm gears can be a bit challenging, and it doesn't have any other physics such as gravity or friction, but sometimes that is a good thing to keep things simple. In addition to linkages, it also has gears, chains, and linear actuators. -
If you don't like the idea of using 'dentist tools' because they remind you of the dentist, then you can use 'wax carving tools' instead: https://www.amazon.com/SE-DD312-12-Piece-Stainless-Carvers/dp/B000SVRSRY/ I have a set of these, and they can be useful for working with Lego, as well as other hobbies such as model making. I also use a crochet hook to help guide string and stretch rubber bands into place when there isn't much room to use my fingers. This stuff is called Plasti Dip, and you can either get it in a spray can, or in a can with a lid so that you can dip your tool into it. For thicker coats, you may have to dip several times to build up the coat and let it dry between coats.
-
Splat changed their profile photo
-
@Aventador2004 - Do you think that ignorance is a valid excuse? Think about it this way: If you want to use an image, did you take that photo and/or create that image yourself? If the answer is no, then you COPIED it from somewhere else. If you do not have permission from the copyright owner, or your use does not fit into the category of the 'fair use' doctrine, then you are not allowed to use that content. The same applies to literary, dramatic, musical, and artistic works, such as poetry, novels, movies, songs, computer software, and architecture. @Jim - Is your comment (quoted above) an admission of guilt? As the copyright owner, I also retain the exclusive right to produce derivative works based on my original, copyrighted image. Given your position on this forum, you should know better, and your blatant disregard for my legal rights as the copyright owner and your continued use of this image and derivatives thereof is very concerning.
-
[MOC] KELP
Splat replied to Nalyd997's topic in LEGO Technic, Mindstorms, Model Team and Scale Modeling
Nice work. The base looks nice and compact, and the coloured plates are mesmerising to watch. It reminds me of @aeh5040's Slithy Troves Kinetic Sculpture Welcome back out of your dark ages!