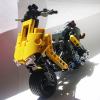
[HELP] Live Axle Geometry
By
piterx, in LEGO Technic, Mindstorms, Model Team and Scale Modeling
-
Recently Browsing 0 members
No registered users viewing this page.
By
piterx, in LEGO Technic, Mindstorms, Model Team and Scale Modeling
No registered users viewing this page.