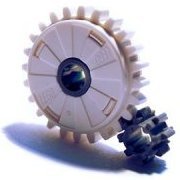
[WIP] Praga Trial Truck 6x6
By
Teo LEGO Technic, in LEGO Technic, Mindstorms, Model Team and Scale Modeling
-
Recently Browsing 0 members
No registered users viewing this page.
By
Teo LEGO Technic, in LEGO Technic, Mindstorms, Model Team and Scale Modeling
No registered users viewing this page.