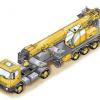
Success 3D printing Technic parts?
By
aminnich, in LEGO Technic, Mindstorms, Model Team and Scale Modeling
-
Recently Browsing 0 members
No registered users viewing this page.
By
aminnich, in LEGO Technic, Mindstorms, Model Team and Scale Modeling
No registered users viewing this page.