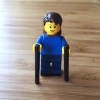
[WIP] MAN TGS 10x8 Effer 2655
By
Beck, in LEGO Technic, Mindstorms, Model Team and Scale Modeling
-
Recently Browsing 0 members
No registered users viewing this page.
By
Beck, in LEGO Technic, Mindstorms, Model Team and Scale Modeling
No registered users viewing this page.