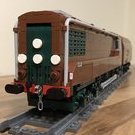
Vehicle Dynamics Laboratory investigates the Castering Effect
By
Hod Carrier, in LEGO Train Tech
-
Recently Browsing 0 members
No registered users viewing this page.
By
Hod Carrier, in LEGO Train Tech
No registered users viewing this page.