Sign in to follow this
Followers
0
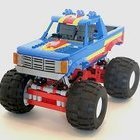
(Help) 4 speed gearbox
By
Oliver 79, in LEGO Technic, Mindstorms, Model Team and Scale Modeling
-
Recently Browsing 0 members
No registered users viewing this page.