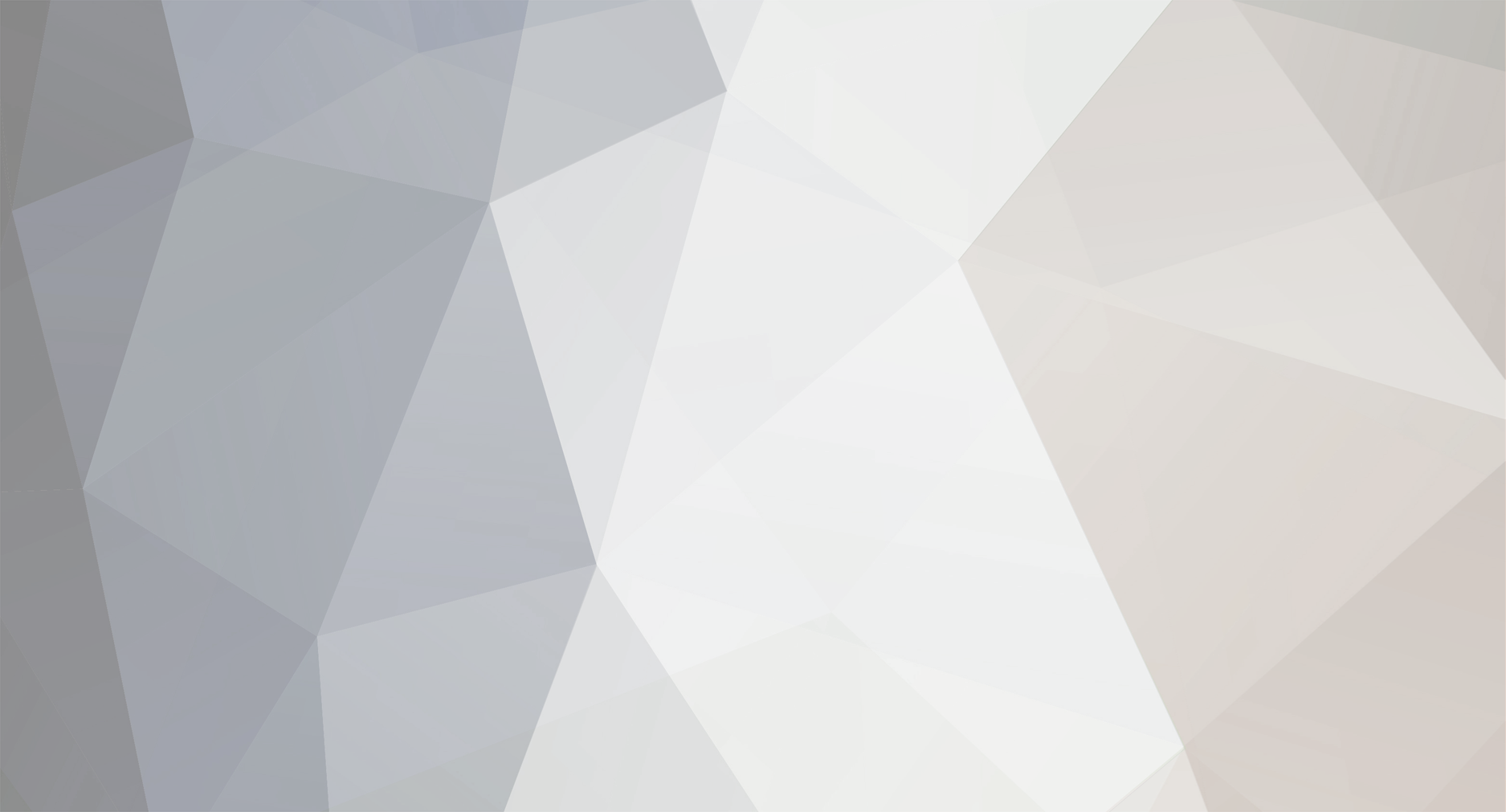
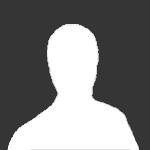
Lucullus
Eurobricks Vassals-
Posts
44 -
Joined
-
Last visited
Content Type
Profiles
Forums
Gallery
Everything posted by Lucullus
-
Front & rear wing are indeed 16stud wide, as I thought it would be covered by the "mirror-rule". The wheels outer center points are exactly 15 studs apart, but I have to admit that I didn't made the "box test". I just assumed that the Mustang rims only protrude one stud. If this is not the case (I can't check it at the moment) it has to be disqualified and I wouldn't have a problem with that because I am sure that a lot of participants kept their entries more thoroughly within the regulations and so it wouldn't be fair. You are right. I did a last minute change from rubber-band suspension to spring suspension and had to ditch the interior therfore. But I wasn't pleased with the interior anyway, because the real car has only one seat very close to the centerline, so it did interfere with the center differential and the HOG-steering, if built in the right position.
-
One thing that has to be kept in mind is, that while the virtual pivot is always located at the intersection of the steering arms it doesn't mean that it will always be at the same place during the steering motion. The wheels won't turn on a circular path like they would do with a nonvirtual pivot. In the above picture this is especially evident if the yellow liftarm is turned so far, that it lies in one line with one of the black ones. In this moment the pivot point is on the 2l axle at the opposite end of the yellow liftarm.
-
Hello everyone. My entry for the Technic Contest 15 is based on the simple idea, that all Lego motors have a too bad power/weight ratio to be used to power a flying object, as long as they stay a part of this object. Therefore I used a Pullback engine to power a simple propeller to make it actual fly. As this alone would be a little too simple I decided to build an aiming/launching mechanism arround the basic concept. The functions are: -tensioning the motor by a worm drive -blocking/releasing the motor -rotating and tilting the launcher
-
Will a pull-back-motor-powered propeller launcher be allowed? Because the actual flying part will be small/simple and not be self-propelled.
- 153 replies
-
- information
- tc15
-
(and 3 more)
Tagged with:
-
Generic Contest Discussion
Lucullus replied to Jim's topic in LEGO Technic, Mindstorms, Model Team and Scale Modeling
Some time ago a "mechanical animal competition" was discussed. Is there a chance that it will be revived? This would require a lot more mechanical creativity from the builders, because you can't just copy the real thing, as is possible with a car / plane. -
Generic Contest Discussion
Lucullus replied to Jim's topic in LEGO Technic, Mindstorms, Model Team and Scale Modeling
Regarding #2, would the requirement "motorized" include a pneumatic animal with external motorized pump, or does it have to be directly motorized? -
"Who will like this set? - builders looking for some breakthrough in Lego transmission design" and "Who won't like this set? - anyone looking for complex and realistic functions" sounds a bit like a contradiction. The Chiron's transmission looks like one of the most complex (and in some aspects, most realistic) Lego features in recent times. In my opinion at least more genious and less "obvious" than the lowered rear diff solution.
-
42083 - Bugatti Chiron
Lucullus replied to Jurss's topic in LEGO Technic, Mindstorms, Model Team and Scale Modeling
Any idea on how those selector rings will be controlled? If each one is connected with two clutches there won't be a neutral position in each "sub-gearbox", so it can't be a simple layout with one clutch-position corresponding to one of the (probably) 8 gears. That means, that the orange selector rings won't move at the same time but are controlled by a mechanism that transfers the 8 positions of the gear lever/paddles to two independent 4 step rotations. -
42083 - Bugatti Chiron
Lucullus replied to Jurss's topic in LEGO Technic, Mindstorms, Model Team and Scale Modeling
The real chiron has a haldex type awd (without center diff), so maybe there will be no diff in the model too but instead clutch gears to connect the front axle to the gearbox. -
42080 Forest Harvester
Lucullus replied to Ngoc Nguyen's topic in LEGO Technic, Mindstorms, Model Team and Scale Modeling
The yellow spiked rollers should be positioned at right angles to the trunk so that it can be pushed up and down. That's how it's done in real harvesters.- 313 replies
-
- 42080
- forest harvester
-
(and 1 more)
Tagged with:
-
FWD Lego Model
Lucullus replied to Legotyres's topic in LEGO Technic, Mindstorms, Model Team and Scale Modeling
Yes i've seen your macpherson suspension but i haven't tested it yet. Did you notice any difference between small and large springs regarding the play between the two tubes of a spring? It seems that at least the large springs have a tendency to bend/wedge instead to compress as they should. I also had the idea to use two big springs connected in opposite direction to improve it but i think this won't work with the wrc's geometry.- 17 replies
-
FWD Lego Model
Lucullus replied to Legotyres's topic in LEGO Technic, Mindstorms, Model Team and Scale Modeling
Current state of my wrc car: As you can see, the gearbox doesn't use selector rings as the "official" Lego gearboxes do. It works a bit like the one in 8860 with an idler gear that can slide along an axle to connect the gears. For that reason it doesn't shift very well when the gears aren't moving. The good thing is, that it has a realistic cone shape. In my previous post i forgot to mention that this is of course an awd drivetrain, but as this car doesn't have a central diff (due to FIA rules), its front axle/gearbox is identical to an fwd one.- 17 replies
-
FWD Lego Model
Lucullus replied to Legotyres's topic in LEGO Technic, Mindstorms, Model Team and Scale Modeling
Hi, i'm currently building a WRC car with the same engine/gearbox/front axle layout as yours (there are some early WIP pictures in the axle collection thread). I think the reason for that layout being so rare is that lego gearboxes (and fake engines) are much out of scale in smaller cars and if you want to position the gearbox next to the engine (as it is done in real cars) it will be even harder at a small scale. My car uses Unimog wheels and it is still very narrow in the engine bay.- 17 replies
-
Is there any chance, that there will be some kind of unique/new/rare feature included in the planning? Something that will set the vehicle apart from the usual "supercar features" which are great but often share the same basic principles like Porsche-inspired gearbox and suspension or Claas-inspired all wheel steering. It's always nice to see some clever door opening mechanism or convertible roof, for example. Different basic concepts are rare, too. Like transverse engine+gearbox layout or a U-shaped front axle as it was used in the Opel Calibra itc. Or fake wankel engine...
-
[MOC] 4x4 Rally Car
Lucullus replied to damjan97PL's topic in LEGO Technic, Mindstorms, Model Team and Scale Modeling
The design reminds me of tajima's Escudo. -
Hello, I made a simple Forklift with the parts from 42043. It was built around 2 of the new pneumatic v2 cylinders that had to be connected and guided in the mast. The thin cylinder from the arocs is used for tilting but it's not connected directly to the mast, to avoid that lifting the load is done by retracting the cylinder (less force than extending). There's one rear wheel mounted on a turntable for steering. It's quite simple, but i hope you like it.
-
Z-bar linkage help
Lucullus replied to jorgeopesi's topic in LEGO Technic, Mindstorms, Model Team and Scale Modeling
I'm not very well at maths, but when i think about your problem (and if i understood it correctly) i end up with nonlinear equations, that could illustrate the correlation between cylinder position and bucket angle. This correlation won´t be proportional, due to the trigonometric geometry of the linkage. If you set the dimensions of the linkage elements as variables, the formula won´t be solvable in a way that it gives you one geometry for a given bucket movement range/speed. So you will have to calculate it seperately for every geometry version. If you have a CAD software with kinematic simulation it may be useful, but i don´t think you will save much time compared to real life testing. Another problem would be, that the maths doesn´t care about bad angles in your linkage, e.g. when the cylinder and the Z link are positioned close to 0° or 180° to each other.