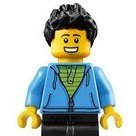
[MOC] 6 Degree of Freedom Robotic Arm
By
Glaysche, in LEGO Technic, Mindstorms, Model Team and Scale Modeling
-
Recently Browsing 0 members
No registered users viewing this page.
By
Glaysche, in LEGO Technic, Mindstorms, Model Team and Scale Modeling
No registered users viewing this page.