-
Posts
2,171 -
Joined
-
Last visited
About Erik Leppen
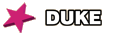
Spam Prevention
-
What is favorite LEGO theme? (we need this info to prevent spam)
<p> Technic and 10242 (yes I know that's a different theme)</p>
Profile Information
-
Gender
Male
-
Interests
Game development, roller coasters, mathematics, LEGO
Extra
-
Country
Netherlands
-
Special Tags 1
https://www.eurobricks.com/forum/public/style_images/tags/technicgear2.png
-
Special Tags 2
https://www.eurobricks.com/forum/public/style_images/tags/technic_bronze.png
-
Special Tags 3
https://www.eurobricks.com/forum/public/style_images/tags/technic_silver.png
Recent Profile Visitors
The recent visitors block is disabled and is not being shown to other users.
-
Nice, a new contest! Seems to be broad enough to allow many entries. Curious what people will come up with this time :) I do wonder what a tracked airplane would look like :D Anyways, I assume a tank counts as a vehicle, even though its main use is not really to transport stuff :P (well, it "transports" bullets really fast, I guess) Also, I assume fantasy vehicles are OK as well. Things don't have to be realistic, right? Not sure I'll have the time to join, but who knows. I never build tracked things, so maybe I should put some dormant parts to use...
-
I'm going to limit myself to sets I built (I have skipped quite a few sets that could be considered great, such as 42009...) and to studless sets (we all know the best sets from the studded era... 8880 supercar, 8480 space shuttle, 8868 air tech claw rig and my persional favorite set ever, 8460 mobile crane) and in no particular order: 8110 Unimog - was a super fun set to build, cool functions, interesting suspension system, one of the better studless models, cool parts (orange was rare back then), pneumatics. 8421 Mobile crane - I love cranes in general, nice array of functions, driven by motor that was part of the set (not optional), some interesting solutions, nice double-acting boom extension. 42054 Claas Xerion tractor - great looks and great functions. A raelly interesting steering mode selector, interesting to build. 8043 Excavator - LOTS of functions in a relatively small space, dense build, interesting to build, interesting switching setup, lots of gears, showed the use of linear actuators perfectly, and a decent size (not overly large) 8258 Crane Truck - Lots of gear-driven functions, large impressive truck, complex folding crane, super fun to build, and the set that best utilized the 5x7 and 5x11 frames which were then new. Especially the Unimog and the crane were sets I was thrilled about when I finally bought them.
-
42213 Ford Bronco SUV
Erik Leppen replied to Ngoc Nguyen's topic in LEGO Technic, Mindstorms, Model Team and Scale Modeling
It might be just me, but it looks like there are #7 angle connectors in the front in black and red, around the headlights. -
This summer wave looks quite nice. The Valkyrie and FXX look splendid. I recognized the FXX and I'm not even really into cars that much. At least it's MUCH better than that yellow car from first-half of the year. The Lambo looks really nice but I'm not interested in RC so that's an easy pass. Also I would have chosen another color. Medium azure would have been cool, or even dark purple. The Ford Bronco looks like a nice set with decent functionality. I also think it looks quite good. I really like that loader. Looks to be full of functions and a true Technic model. The excavator looks very interesting mechanically and I'm curious what's 'under the hood', but there's no way in a thousand years that I'm going to spend 400 euros on this. The mars rover looks... weird. It reminds me of the Space subtheme from last year. But it does seem like a nice little set. I don't really care for the muscle car (that's apparently from a movie). It's modelled nicely I think, it seems to have decent functionality, and a really cool drift function, but it doesn't interest me enough to spend the money on this. I think I might get that Valkyrie for the dark turquoise parts, and order a bunch of the Bronco's tyres separately. I want those tyres :D
-
LEGO.com & Online Ventures Discussion
Erik Leppen replied to Brick900's topic in General LEGO Discussion
What's so terrible about it? -
I don't use a formula, but I did start weighing sets I buy, and then I mean the assembled model (because the packaging and instructions are of no value to me.). Seeing if I got good value. Currently the Mona Lisa has by far the best weight-per-price of the 6 sets I did this for so far. Also, of course, I find it a real treat that the number of pieces is now on the boxes of sets. That makes comparing price-per-piece much easier. Of course, the 10 cents per part (€) is not a hard limit, but with a photo of the model you can make a decent estimate of what kind of pieces there are and if they are of decent size. I mean, weight-per-part is not entirely correct either, because 2 small pieces give more MOCing options than 1 large piece that is essentially those two combined. With MOCing you usually need both small and large parts, so the best estimate is somewhere in the middle of price-per-piece and price-per-gram. A second thing I do now is check the distribution of the colors of the parts in a set. I recently bought the large Milano spaceship set, because I liked the ship and it seemed interesting to build and reviews were good, but in the end I buy for parts. I was a bit disappointed because the actual number of blue and orange parts is actually very limited. It's almost entirely gray and dark-gray. I could have known that beforehand, had I just checked the inventory better. So since then, when I see interesting sets, I wait until the inventory is available and I count the numbers per color. That gives me an indication of whether the set contains a good chunk of parts in colors I am interested in. Because, well, I don't really have a shortage of gray and black. How different, for example, is the large Simba sculpture, which is a great source of bright light orange, and has a few tan bits I want too. Generally, for me personally and at this moment: the fewer gray and black bits, the better.
-
Brickshelf is shutting down. Let's try to save it.
Erik Leppen replied to Trekkie99's topic in General LEGO Discussion
I have all my stuff on brickshelf, but my main concern is not the files. I have my files locally. My main concern is the broken links everywhere. I don't know if anything could be done about that though. If the URL goes down, all links to it will become dead links, I guess? (I'm not really into web-development so I don't know.) -
I don't know. Years ago, I tried using this connection of inserting a bar in one of the holes, and I believe I never got the parts separated again. It could be that the bar was transparent though (back from when transparent pieces were a different material), but not sure. In any case, I avoid the connection ever since. (I actually never needed it since.)
-
For the bodywork, I had to look a bit longer to notice it was even different, but under the hood this seems pretty innovative. Bodywork-wise, I think the options are a bit limited, so I understand you went with this type of car. But this model does suffer a bit from the fact that on first glance, it looks like a variation on the official set, where actually, it is a complete rebuild. The chassis design looks really clean and I really like the suspension setup. It looks to be pretty interesting to build and totally different from the original set. I also like how you put a more standard gearbox in this, instead of all those levers of the original set. Yeah, all in all it seems like a technically interesting and well-designed model, without any 'messy bits'.