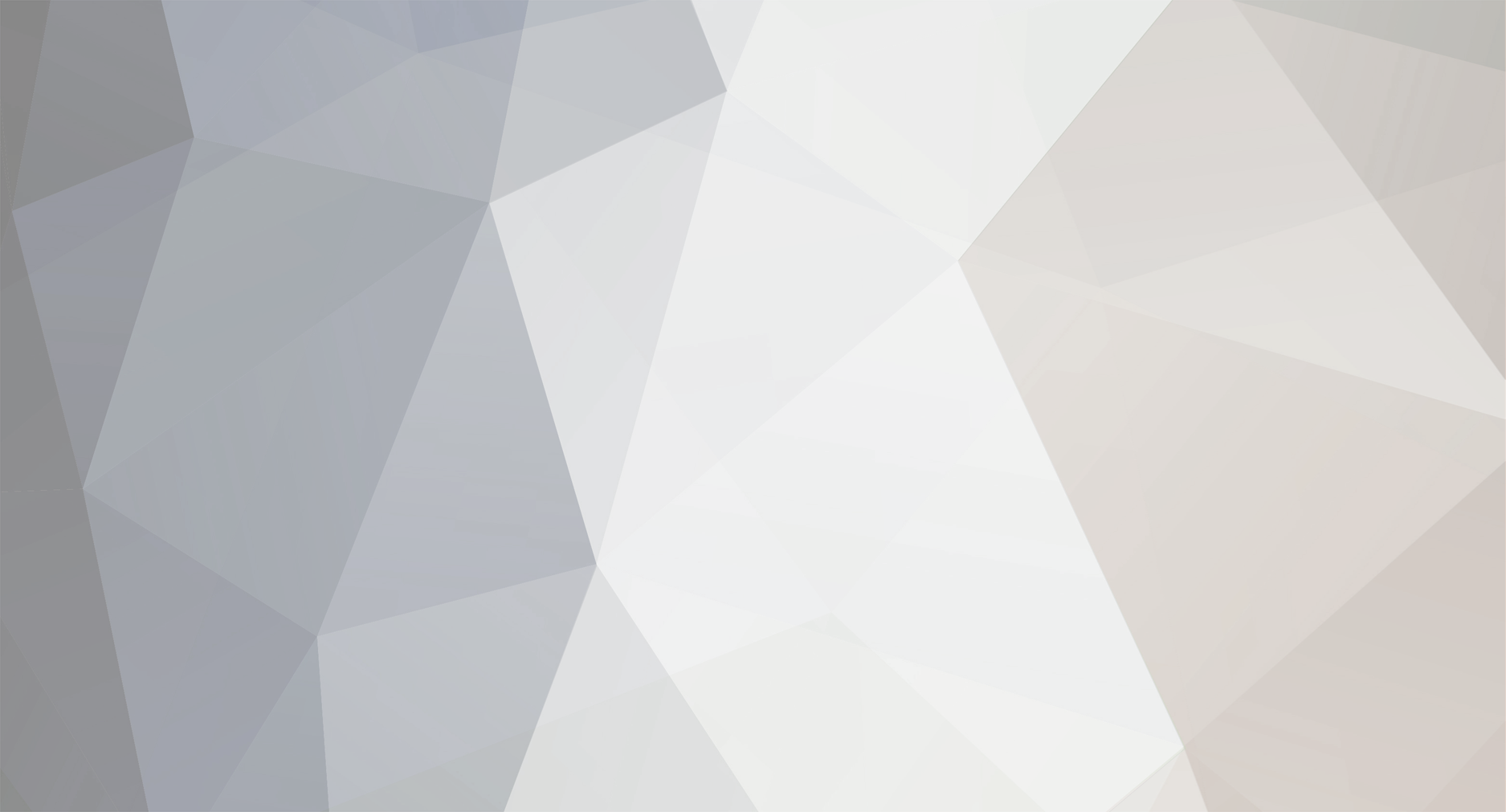
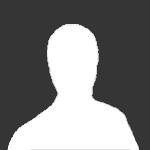
Josephiah
Eurobricks Citizen-
Posts
214 -
Joined
-
Last visited
-
[TC21] Plymouth SuperBIRD
Josephiah replied to 2GodBDGlory's topic in LEGO Technic, Mindstorms, Model Team and Scale Modeling
Loving the concept, the complexity, and the execution of this! Some lovely mechanisms in the, combined with some nice sculpting. If I may make one tiny suggestion: I think your entry video would be much improved by showing the transformation up front - at present the viewer has to search through 12 mins of gear/mechanism close-ups to find the real highlight! -
I've heard that ABS becoming one of the leading filaments in the industry was largely an accident, i.e. it just happened to be first, rather than being inherently great - and it's enduring popularity is a bit of a mystery to me. At my work we basically skipped ABS entirely and went straight to PETG - much better all round. Good strength, easy to work with, and less brittle than PLA. Others I know also swear by ASA for ABS-like properties with less fuss, but I haven't tried that myself.
-
Laws on battery accessibility are definitely tightening up - at my engineering consultancy we've had clients asking us for product design adaptations, looking towards upcoming regulation changes. In those cases, though, it has tended to be around product which use the small "button" or "coin" lithium batteries, which can cause horrific injuries if swallowed.
-
We have a couple of Prusa i3 filament printers at work (used a lot for several years), and a new SL1 resin printer (not used much yet). I haven't tried doing technic parts - as you say, the tolerances will be a challenge. I have had reasonable success with printing Duplo parts (well, actually, adaptor pieces from Duplo to Brio train tracks - worked really nicely with a bit of trial and error). I don't know if you might want to try a finer nozzle than the 0.4mm one many printers come with by default? Don't bother with ABS (it's ubiquity in the 3d printing world was largely a matter of just being there first) - PETG is my go-to material at the moment - it's stronger than PLA, and less brittle - it has a bit of flex to it. Friends recommend ASA as well, though I haven't tried it myself. One of the biggest challenges with 3d printing is getting the directionality right for any given part - you really have to think through what direction the stresses will be going through the part - if the forces on it are in a direction that makes the layers want to separate, then consider printing in with the layers in a different direction. And sometimes the best solution for a particular part is to print in two halves (to get a nice flat plane to put on the printed) then glue together. With a bit of trial and error you can even peg/glue parts together with short pieces of raw filament. My limited experience with resin printing so far suggests great surface finish, detail and appearance, but with a tendency to sag/warp in the printer if not supported well enough (so we've often found the dimensional accuracy worse than our filament printers), and the materials tend to be a little more brittle. In terms of the mail-order services, we've had good results from Materialise (both the full on commercial (expensive!) service for work, and the more accessibly-priced consumer version); haven't tried Shapeways, so would be interested to hear people's impressions. Have fun experimenting - will be interested to see how you get on.
-
Hi guys, This week my boys had a special treat as we brought my old 8485 set out of the garage so they could build the T-rex. Everything is in surprisingly good condition, except for a couple of the flex system cables, which are a lot more brittle than they were 25 years ago and have not survived the building process. (These were always fairly weak parts, I know, but they are definitely worse than I remember!) So the question is: has anyone discovered any way of mending them? Or replacing them in some way? (I have ordered a couple of spares from bricklink, but I don't expect them to last particularly long either, as they are just as old...) Thanks in advance!
-
Josephiah started following Lego Mindstorms EV3 Monorail
-
Lego Mindstorms EV3 Monorail
Josephiah replied to Hanso's topic in LEGO Technic, Mindstorms, Model Team and Scale Modeling
Just stumbled across this project, and I love it! Particularly like the way the switch track flexes as it moves. Do the train and the switch tracks interact with each other? In other words, does the train "know" the status of the switch, and vice versa? I also like the versatility of the tiled track system with the colour sensor - adding a slow down area or a station is as easy as swapping a couple of tiles.- 44 replies
-
- mindstorms
- trains
-
(and 2 more)
Tagged with:
-
Technic 2019 Set Discussion
Josephiah replied to dimaks13's topic in LEGO Technic, Mindstorms, Model Team and Scale Modeling
Depends whether it has a crane on it or not! -
We use it for prototyping stuff fairly often at work, especially for fast iteration around mechanism design. Complex hand tool mechanisms, an adjustable wind turbine blade, bits of a wheelchair, a folding table mechanism, even a new type of horse saddle... (Unfortunately not stuff I can readily share as pictures, as they now form parts of our clients' IP!)
-
As a few have commented further up the thread, the seemed to be a change of insulation material for the sets around 1996/7 (shuttle/bar code truck) to the matte/rubbery textured stuff which was particularly bad. I have plenty of earlier wires (shiny finish, like in 1995's control centre II) which are in much better condition.