-
Posts
2,426 -
Joined
-
Last visited
About doug72
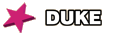
- Birthday 03/31/1947
Spam Prevention
-
What is favorite LEGO theme? (we need this info to prevent spam)
To build technic and GBC and interact with other forum users
-
Which LEGO set did you recently purchase or build?
Spider Crane
Profile Information
-
Gender
Male
-
Location
South Shields - Tyne & Wear
-
Interests
Cycling, Railways, Industrial Archaeology
Extra
-
Country
England, UK
-
Special Tags 1
https://www.eurobricks.com/forum/uploads//gallery/album_241/gallery_8966_241_2675.png
-
Special Tags 2
https://www.eurobricks.com/forum/public/style_images/tags/technicgear2.png
Recent Profile Visitors
8,744 profile views
-
I did 1 hr of testing with good results, train did not ever fail, I will do some more testing soon. @doug72 I can do some PDF instructions (should be a little bit better then the last ones) for you if you want to build it and have a look. Thanks Looks to be more robust & reliable module.. Yes please make PDF instructions & I will build it. At the moment I am struggling with trying to make a passing loop module for Type 2 GBC Train car.
-
Thanks for the new instructions. forGBC Train type 2. Followed your instructions all went OK until the the change over switch seem to stop working. Problem finally found, it was due to the insulation of the PF cable from the L motor had broken down & bare wires were toucing. It is hard to route the PF cables so as not to interfere with the two trip beams & the switch change over links. Also if the trip rubber bands on the train reverser are too strong it tend pushes the cross axle at the none switch end of the battery box through the trip beam due to low friction where it passes through the axle holes. Had resorted to glueing the axle to try & stop this happening. Rebuilting from the start again and try & improve try & PF cable runs .
-
PF receiver not working
doug72 replied to Sentinel's topic in LEGO Technic, Mindstorms, Model Team and Scale Modeling
Before cutting wires, check out the contacts on the cable plug and PF rx are making contact with each other. Just ease out the contacts on the plug & PF Rx. and test. Its worked for me. -
MOC - World's largest engine
doug72 replied to Duca59's topic in LEGO Technic, Mindstorms, Model Team and Scale Modeling
An excellent build of a large Marine Diesel Engine, I was a Chief Marine Enginner on VLCCs for most of my time at sea, now retired. Just one thing missing: the barring over motor & gear to turn the engine over before starting up on air to ensure all parts free & lubricated etc. The largest engine built is a 14 cyclinder made by a Finish Company. https://en.wikipedia.org/wiki/Wärtsilä-Sulzer_RTA96-C A big challenge would be to build a Doxford opposed piston Engine. A Nightmare to work on. -
Train GBC - Back on track.
doug72 replied to doug72's topic in LEGO Technic, Mindstorms, Model Team and Scale Modeling
My self unloading ball hopper allows for 30 balls to transfer to any GBC module with the standard inbox 10L height. -
Train GBC - Back on track.
doug72 replied to doug72's topic in LEGO Technic, Mindstorms, Model Team and Scale Modeling
GBC Train:- I have reviewed your suggestions but I dought any of them would meet the criteria for GBC TRAIN modules. The Train Car with its ball hopper is the heart of any module by using the train car to power the module and the train reverser. More complex Train GBC modules are possibly using EV3 to power & control them. I am currently have an early stages WIP for a new module to transfer a ball hopper to another train car or to ground level to load balls from an GBC Inbox. -
Recently I have been dismantling some older GBC Train modules that used these gear racks. Dispite carefully disconnecting them, many of the yellow ones were found to have split 0r cracked end connections. Tried gluing the crack ends without success. Black gear racks don’t seem to have this problem. Possibly yellow ones are made from a different material. Has anyone found a use for the broken ones ?