-
Posts
479 -
Joined
-
Last visited
About coaster
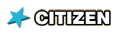
Spam Prevention
-
What is favorite LEGO theme? (we need this info to prevent spam)
Trains
Contact Methods
-
Website URL
www.bricktracks.com
Profile Information
-
Gender
Male
Extra
-
Country
USA
Recent Profile Visitors
6,069 profile views
-
BrickTracks: different curves, PF/9V compatible
coaster replied to JopieK's topic in LEGO Train Tech
Hi @Ts__, I can send you a couple replacement switch stands and base pieces if you like. The switch stands only are meant for 180° of rotation though, so forcing it beyond that will indeed snap those linkages. Email me at info@bricktracks.com. -
BrickTracks: different curves, PF/9V compatible
coaster replied to JopieK's topic in LEGO Train Tech
It is a known issue that can occur on the first batch of switches that went out. We've since resolved the problem, but the good news is it's easy to fix. I will post a video on the repair in the next few days. -
The wheel flanges are 1 plate tall, so you are correct, add 2 plates/6.4mm in diameter. @supertruper1988 is working on the .dat files, but there are lot of them, so it's just taking a bit to get it all together. Plus, he's in the middle of moving across the country. I would help with it, but I'm dumb and don't know how to properly build the .dat file. My method is to export the CAD model into Part Designer and then export to Stud.io, but the file sizes are comparatively massive.
-
The problem with smaller flanges is you ride on the flanges when crossing another rail on a switch for instance. The rail has to break to allow movement on the crossing path, so to prevent bumping there is a raised area that supports the flange. If you go smaller, it will be fine most of the time, but you'll have a definite bump on such crossings. Also, are we assuming you are going flanged-blind-flanged, with the wheels as close together as possible?
-
Increasingly losing patience with Lego
coaster replied to SteamSewnEmpire's topic in LEGO Train Tech
Since I like to build 1:38, I compare them to LGB. I'm way ahead then! -
BrickTracks: different curves, PF/9V compatible
coaster replied to JopieK's topic in LEGO Train Tech
We've already blasted through our first batch of switches, but don't worry, the second batch is due any day now. New orders will be a couple weeks though before they ship. -
+1 Like. LEGO doesn't mind this at all. They're well aware their offering is lacking, it's just not profitable enough for them to pursue it. They are perfectly fine with the various 3rd party suppliers picking up the slack.
-
Trixbrix R56 curves injection molded recommendation
coaster replied to koraldon's topic in LEGO Train Tech
Hi koraldon, send me an email at info@bricktracks.com. We can work something out. :) -
BrickTracks: different curves, PF/9V compatible
coaster replied to JopieK's topic in LEGO Train Tech
All the pieces are finally here! We're assembling the kits as fast as we can, but there are a ton of pre-orders, so it will take a few days to get through all of these. I quite literally need to build thousands of switches. I plan to have everything out early next week. -
BrickTracks: different curves, PF/9V compatible
coaster replied to JopieK's topic in LEGO Train Tech
Hi All, sorry I haven't kept up with the EB updates like I should have. The ratio of interactions I have here vs. Facebook is considerable. Just to update everyone, barring another winter storm (which, we look to be getting this weekend and early next week, so who knows), we are looking good for a March 1st availability. Pre-orders will be going out in the order they were received, with HA Bricks and Brickmania's shipments going out first so they can distribute to their customers. There is a sizeable number of pre-orders, so it will likely take a couple days to get them all out, but everything should be out the door by the 1st. -
A review of the first elements from the FX Track system
coaster replied to zephyr1934's topic in LEGO Train Tech
I don't think the pricing is out of line. It was a touch higher than I was guessing, but not by much. Unfortunately for all of us, none of us are in a position to be truly mass-producing tracks; either mine nor FX. If we were selling our stuff in every Walmart and Target and every other big box retail store, where we're moving hundreds of boxes a day, then sure, it could be and would have to be a lot cheaper. But we're unfortunately a small niche within a niche, with barely enough demand to warrant tooling (and even that is often questionable).- 199 replies
-
- wide radius curves
- 9v
-
(and 2 more)
Tagged with:
-
The Chicago Aurora & Elgin Railroad provided interurban service from downtown Chicago to the western suburbs, branching off at Wheaton either north to Elgin or south to Aurora. Sadly, the railroad ceased operation in 1957, but the right of way was preserved as a walking/biking trail. Remnants of the railroad can still be seen along the trail. Several of the interurbans themselves have been preserved at local museums, so here is my take on #308: I build in 1:38 or "10-wide" scale, and it is indeed 10 studs wide and approximately 54 studs long. It is driven by 2x 9V motors controlled by a PF IR-receiver and rechargeable battery, and the headlight at each end works, too. Aside from the decals, it is completely purist. What I enjoyed most about this build was that it utilizes parts from all different eras. The white windows are the old style 1x3x2 windows from the 50's, up to small structural elements just released last year, and everything in between. The thin red stripe above the windows is brick built, made from 2x2 hinge top plates. To account for the 1/4 plate offset, this is repeated in grey at the roofline. Unfortunately, there is no interior to these. The older windows and bricks have notoriously poor clutch, requiring quite a bit of internal structure to keep the roof in place and the windows themselves from falling out. Of course, the first rule building a model is "why build one when you can have two at twice the price?", or in this case, three: #309 and #316 are just trailers, but are each uniquely different in their build, as their real-life counterparts were actually built by three different manufacturers, but to very similar specifications.
-
Awesome, thank you!
-
Thanks, but sadly I don't. It was built almost 10 years ago now. I probably had an MLCad model of it, but it's long since gone or lost. It actually is pretty simple though. The road bed is an overlapping stack of 6x12 plates, a total of 2 plates thick. Technic beams run along the top and bottom, so you have the correct spacing for locking both with the vertical beams. The rest is just 3-4-5 triangles. PM me your email address and I'll take some extra pictures for you.
-
Hi @Alban Nanty, any chance you could add the BrickTracks track pack as well? While similar, there are some difference from the TrixBrix versions. The folder can be downloaded from the BrickTracks site, but it would be nice to have it available from BlueBrick as well. https://www.bricktracks.com/resources Thanks!